News
Part of the Cluster Hub “Production of raw materials for batteries from European resources”, the RHINOCEROS consortium received the online visit of FREE4LIB representatives during the second day of the Consortium meeting held in Gothenburg. This initiative including stakeholders involved in different European R&D initiatives goes beyond building a knowledge exchange ecosystem to address common topics related to EU-funded projects; it paves new collaboration routes and synergies aiming at driving innovations for the recycling of batteries and the production of raw materials for battery applications from primary and secondary resources available in Europe.
Represented by Julius Ott (industrial engineer with expertise in circular economy at Karl-Franzens-Universität Graz) and Pau Sanchis (senior policy officer Eurobat), the FREE4LIB presentation focused mainly on the Digital Battery passport and the relevant legislative situation at European level.
Pau Sanchis referred to the Digital Battery Passport in the context of the new regulation on batteries and waste batteries which entered into force on 17 August 2023. According to this update, thoroughly explained in Art. 77, the battery passport should contain information “relating to the battery model and information specific to individual battery, including resulting from the use of that battery”.
“Batteries should be labelled in order to provide end-users with transparent, reliable and clear information about batteries and waste batteries. That information would enable end-users to make informed decisions when buying and discarding batteries and waste operators to appropriately treat waste batteries. Batteries should be labelled with all the necessary information concerning their main characteristics, including their capacity and the amount of certain hazardous substances present. To ensure the availability of information over time, that information should also be made available by means of QR codes which are printed or engraved on batteries or are affixed to the packaging and to the documents accompanying the battery and should respect the guidelines of ISO/IEC Standard 18004:2015. The QR code should give access to a battery’s product passport. Labels and QR codes should be accessible to persons with disabilities, in accordance with Directive (EU) 2019/882 of the European Parliament and of the Council (17).”
The policy officer emphasised the role of the standardisation process on the Battery Passport, which requires the Commission to adopt implementing decision requesting European Standardisation Organisation to develop standards in support of Ecodesign by December 2023. Standards regarding the technical design and operation of the Battery Passport are expected to complement provisions under Art. 78. According to the timeline presented in the regulation, the first application of the battery passport is expected in 2027. From 18 February 2027 onwards, “all batteries shall be marked with a QR code as described in Part C of Annex VI.
The new regulation aiming at strengthening sustainability rules for batteries and waste batteries will be supported by various secondary legislation pieces which will ensure all the requirements will be developed and implemented effectively. The QR code shall provide access to the following:
- for light means of transport (LMT) batteries, industrial batteries with a capacity greater than 2kWh and electric vehicles batteries, the battery passport in accordance with Article 77.
- for other batteries, the applicable information referred to in paragraphs 1 to 5 of this Article, the declaration of conformity referred to in Article 18, the report referred to in Article 52(3) and the information regarding the prevention and management of waste batteries laid down in Article 74(1), points (a) to (f).
- for starting, light, and ignition (SLI) batteries, the amount of cobalt, lead, lithium or nickel recovered from waste and present in active materials in the battery, calculated in accordance with Article 8.
The policy overview presentation was complemented by the technical presentation undertaken by Karl-Franzens-Universität Graz, that will develop a data model of the digital battery passport platform aiming to close the information gap between beginning-of-life (BoL) and end-of-life (EoL) battery lifetime. Relying on knowledge generated previously by Univ. of Graz, the researchers set an objective to define clear user roles and establish access to certain information. Up to this moment, the work carried out has been focusing on data collection and data handling (data points sorting) on the other side. This specific work encountered various challenges, notably the users willingness to share information, process standardisation, the variety of products, the recycling cost/revenue ratio, the dynamic development of the legislative framework, to name a few.
Learn more about the progress on the battery passport on the FREE4LIB website.
The modified Black Mass (BM) obtained in Task 4.4 – Reactive milling for the production of metallic black mass (MBM), as well as the BM supplied by partner ACCUREC (ACC) were leached under different conditions to extract lithium (Li) salt.
The BM provided by ACC consists of graphite, as well as transition metals such as nickel (Ni), manganese (Mn), cobalt (Co), along with their respective oxides and impurities – copper (Cu), iron (Fe), and few fluorinated compounds. Li is present in the form of lithium carbonate [Li2CO3] and lithium aluminium oxide [LiAlO2 ]. However, breaking off LiAlO2 to a soluble Li-salt and removing fluoride contamination is a challenging process. To overcome this, the BM was heated with calcium hydroxide in deionised water for one hour and then filtered.
Illustrated in the next figure, LiAlO2 decomposes during heating and transforms into insoluble calcium aluminium hydroxide. Dissolved fluoride anions are caught by Ca2+ ions and precipitate as calcium fluoride. The soluble part only contains Li- and Ca-salts. The latter can be transformed into calcium carbonate and removed with a second filtration step.
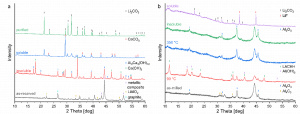
X-ray diffraction patterns of leaching and purification process. a) black mass supplied by ACC and treated with calcium hydroxide. b) aluminium system of modified black mass
The second BM from partner TES, obtained after ball milling, consists of graphite, the metallic composite, lithium oxide and the oxidized reducing agent, along with some impurities like Fe and fluorinated compounds.
Lithium extraction after ball milling
In the aluminium system, the extraction of lithium salt poses certain challenges. Due to the tendency of residual aluminium powder to ignite when in contact with air, this requires cautious handling. During milling lithium aluminium oxide is formed, and in the basic solution, a significant amount of aluminium hydroxide dissolves and reacts with lithium hydroxide and CO2, resulting in the formation of a poorly soluble compound called LACHH. To address this problem, the suspension is heated to 90°C to reinforce the reaction between aluminium hydroxide and lithium hydroxide. The LACHH formed can be decomposed at 350°C into insoluble aluminium oxide and soluble lithium carbonate, which can be separated through filtration.
Lithium extraction in the calcium system, on the other hand, is a relatively straightforward process. The milled powder shows low reactivity towards both oxygen and water. Scientists successfully extracted 98% of lithium from the black mass; however, calcium hydroxide was also dissolved in the process. Subsequent purification steps led to the isolation of lithium carbonate with a purity of 93% in a yield of 75%. The main impurities are shown in the figure displayed below.
In the upcoming months, researchers will work to improve the leaching conditions towards a lower reagent and water consumption, while obtaining a higher purity of resulting lithium salt and lower lithium loses during purification steps.

Impurity cations in isolated lithium carbonate from the calcium system of modified black mass
During the second semester, researchers from KIT further studied and improved the conditions for the mechanochemical transformation of Black Mass (BM). With the BM supplied by ACC is already in a reduced state, the focus now shifts towards reducing the BM provided by partner TES.
This BM consists mostly of nickel-manganese-cobalt (NMC) cathode material and graphite, and it was found to cause a longer reaction time. It is expected that the graphite exfoliates during milling and creates thin protective layers around NMC particles and the reducing agent, slowing down the reaction kinetics.
Using variations of milling parameters like ball-to-sample ratio or the type and amount of reducing agent, researchers optimised the process towards the fastest kinetics. During the investigation, no intermediate reduction to transition metal oxides in lower oxidation states was observed. However, the full reduction of the respective part to the metallic composite occurred.
The operation took place in a shaker mill, and it requested an excess of 3.3 equivalents of Aluminium (Al) towards NMC was required to attain a complete reduction within a reasonable time. This transformation was accompanied by the formation of aluminium carbide and the presence of residual fine aluminium powder which caused a self-ignition hazard when the milled powder came into contact with air.
In contrast, when using calcium as a reactive agent, researchers observed a fast reaction but they also reported a strong dependency of reaction kinetics on calcium size. The hazard of self-ignition when exposed to air was limited in this case by using stoichiometric amounts.
In addition, the research team has been conducting preliminary experiments for the scale-up process using a planetary mill. It was observed that the choice of the milling type has a significant impact on the reaction kinetics. Attempts to crush calcium pieces proved to be unsuccessful, therefore not initiating any reaction. However, when using aluminium, reactions occurred much faster.
In the months ahead, the research team working in WP4 will continue to investigate the milling parameters for the planetary mill.
Find out more information about the activities developed in WP4 in the article Reactive milling for the production of metallic black mass (MBM) – Rhinoceros project (rhinoceros-project.eu)
Read more about the black mass leaching operations in the article Materials extraction and direct routes for the synthesis of electrode materials: Recovery of Lithium as battery grade materials
Three dimensional (3D) Scanning of Battery Packs
Following the manual dismantling of various battery packs during the first six months of project, researchers at University of Agder (UiA) have developed a semi-automated process to address the diverse nature of battery packs. Their advanced robotic system can estimate the size of individual components of a battery pack. Afterwards, using different angles, it identifies optimal locations to capture precisely 3D images of these components, thus ensuring no detail is missed through this comprehensive scanning.
Using different perspectives, this thorough scanning process is further translated into a list of point clouds. Applying sophisticated algorithms, these point clouds are later combined and merged into a solid mesh component. This process is repeated individually for each new component which needs to be scanned.
Beyond geometric characteristics
While geometric characteristics are important, they provide even greater value when combined with other physical attributes and interconnection data of the components. The researchers have successfully documented these details, resulting in a rich digital repository of the battery pack. With the establishment of this detailed digital repository, the focus is now shifting towards its applications, where the primary goal is to automate the disassembly sequences.
Simultaneously, the team is also focusing on the automatic characterisation of battery packs and modules. Significant efforts are channeled towards creating a robust digital simulator, which will serve as a platform for training and rigorous testing of the disassembly planner – currently under development.
Innovation in disassembly tools
At the same time, the research team involved in work package 3 have been working on improving the disassembly operations tools. The results reported positive feedback, with several tools already successfully tested in lab environment. This is a significant step towards the fully automated disassembly process.
A noteworthy development is the automation of the non-destructive disconnection of cables. This procedure is essential as it stands as the second most frequent operation in battery pack disassembly, just after the unscrewing operation.
You can read more about previous activities developed in work package 3 in the article ‘Manual dismantling of a battery pack‘.
The Gas-Diffusion Electrocrystallisation (GDEx) technology allows the one-step recovery of metals and synthesis of new materials with high added value. In the framework of the RHINOCEROS project, the research team at VITO has been focusing on optimising the GDEx technology to achieve selective recovery of nickel (Ni), manganese (Mn), and cobalt (Co), contained in leachates from black mass.
Currently, researchers at VITO are working the development of material libraries based on the different Ni-Mn-Co ratios in the precursor stream, studying the different stoichiometries and crystallographic structure of the new synthesised products, e.g., spinel and layered materials. Moreover, their research extends to the investigation of black mass Ni, Mn, Co recycling procured from consortium partners.
Following work will consist in testing the upcycled products from black mass as new cathode materials for Li-ion batteries.
You may be interested also in the article “Materials extraction and direct routes for the synthesis of electrodic materials“.
More information about the GDEx process can be found at http://gdex.vito.be
On Monday, 10 July 2023, the Council of the European Union adopted a new regulation that strengthens sustainability rules for batteries and waste batteries. This regulation covers the entire life cycle of batteries, ensuring their safety, sustainability and competitiveness from production to reuse and recycling.
Read the official press release
Recognising the vital role batteries play in the decarbonisation process and the transition towards zero-emission mobility, Teresa Ribera, Spanish Minister for the Ecological Transition reinforced the Presidency’s commitment to supporting comprehensive regulation encompassing all types of batteries. This includes waste portable batteries, electric vehicle batteries, industrial batteries, starting, lightning and ignition (SLI) batteries primarily used in vehicles and machinery, as well as batteries for light means of transport like electric bikes, e-mopeds, and e-scooters.
“At the same time end-of-life batteries contain many valuable resources and we must be able to reuse those critical raw materials instead of relying on third countries for supplies. The new rules will promote the competitiveness of European industry and ensure new batteries are sustainable and contribute to the green transition.”
| Teresa Ribera, Spanish Minister for the Ecological Transition
To foster a circular economy, the regulation establishes requirements for the end-of-life phase, including collection targets and obligations, material recovery targets, and extended producer responsibility. Dedicated collection objectives for waste batteries used in light means of transport will be implemented, aiming at 51% by the end of 2028, respectively 61% by the end of 2031. Furthermore, the regulation sets mandatory minimum levels of recycled content for industrial batteries, SLI batteries and electric vehicle batteries. The following initial values have been established:
- 16% for cobalt
- 85% for lead
- 6% for lithium
- 6% for nickel
Additionally, batteries will also be required to hold documentation proving their recycled content.
To improve the functioning of the internal market for batteries and ensure fair competition, the regulation introduces safety, sustainability, and labelling requirements. It includes provisions for battery labelling and information disclosure, including details on battery components and recycled content. Additionally, an electronic “battery passport” and a QR code will be implemented to enhance traceability and transparency. These labelling requirements will take effect by 2026, while the QR code implementation is expected by 2027, providing member states and manufacturers with ample time to prepare.
This new regulation aims to mitigate environmental and social impacts throughout the battery’s life cycle. By establishing strict due diligence rules for operators, the EU is ensuring operators are bound to verify the source of raw materials used for batteries placed on the market. However, the regulation provides for an exemption for SMEs from the due diligence rules.
After its signature by the Council and the European parliament, the new regulation will be published in the EU’s Official Journal, expecting to enter into force 20 days after.
RHINOCEROS project in the current legislative framework
Launched in 2022, the RHINOCEROS project fits within the current framework recently adopted by the Council of Europe under the Spanish Presidency. Designed to support the raw materials supply, the RHINOCEROS project will demonstrate a smart sorting and dismantling robot at TRL6, enabling the automation of a battery repurposing production line. When direct reuse and repurposing of batteries is not possible, RHINOCEROS will investigate several ground-breaking circular recycling routes aiming at the recovery of all materials present in LIBs (e.g., metals, graphite, fluorinated compounds, electrolytes, polymers, and active materials).
A first set of conclusions stemming from the research of our partners generated a database and the parameters for module selection, which will further facilitate the development of electric vehicles 2nd life batteries.
Read more in the article “Acceptance criteria and guidelines for 2nd life prone LIBs”
The infographic can be accessed on the Council of the European Union’s website using this link.
After a successful cluster workshop organised in November 2022, during the Raw Materials Week, RHINOCEROS, together with other seven European projects, set the foundations of the hub carrying the same name: “Production of raw materials for batteries from European resources“. In 2023, the hub welcome two new members and today, the community can count on the involvement of ten European projects.
The platform is a knowledge exchange ecosystem where partners involved in different European projects can work together to push innovation further and make sure the novel technologies developed will become sooner part of our daily lives. The platform facilitates collaboration among research institutes, industry and innovation stakeholders driving the recycling of batteries and the production of raw materials for battery applications from primary and secondary resources available in Europe.
Mission and Objectives
- Expand the network and provide exploitation opportunities
- Organise forums to discuss common issues (both technical and/or non-technical)
- Build up a network to provide joint input to the European Commission and identify future challenges that need to be addressed
- Foster new innovations Discover new approaches and process, and therefore new insights to be developed
Aiming towards a zero-waste strategy for the recovery of metals from battery refining waste waters, LEITAT is working on the development and evaluation of novel polymer inclusion membranes (PIM). PIMs are a type of liquid membrane in which the liquid phase, the extractant, is held within a polymeric network. The interest in these membranes has been growing exponentially over the past few years as an alternative separation technique to conventional solvent extraction.
Work during the first six months has focused on the evaluation of different extractants for the target metals: lithium, manganese, cobalt and nickel. Researchers established a liquid-liquid extraction protocol based on two different processes in which the target metal is extracted and recovered separately. During the extraction step, a specific carrier compound selective towards the target metal separates an amount of it from a feed metal solution. The recovery of the metal takes place in the second process, where a stripping solution is employed to recover the metal previously extracted through the carrier. Initial PIMs containing the most efficient extractants have been prepared, characterised and are currently evaluated. The featured image depicts the continuous procedure used to test the synthesised PIMs.
The current industrial pre-treatment and downstream processes (e.g., pyrolysis, calcination, etc.) are still inefficient and have significant limitations. Plastics and electrolytes sacrificed in the initial stages of the recycling process are overlooked when it comes to their recovery. Within the RHINOCEROS project, Chalmers University [CHA] is working on recycling of ignored content of the LIBs waste, electrolyte and polymeric materials by developing an innovative process based on Supercritical Carbon Dioxide (sc-CO2) technology.
Due to its environmental friendliness, non-toxic, low cost and straightforward processing features, the sc-CO2 technology has been attracting both scientific and industrial interest. With consistent leverage over other processes, sc-CO2 technology is already widely used in various industries including food, cosmetic and pharmaceutical industries [i.e., to decaffeinate coffee or tea, extract vegetable oils etc.] Although it has many applications, its use in battery recycling was recently discovered and the Chalmers research group is one of the pioneers in this field.
Within the project’s framework, CHA researchers are targeting the development of the sc-CO2 extraction process which will selectively recycle the electrolyte and the polymeric material from the LiB waste. The electrolyte, binder, and separator will be recycled in subsequent steps and purified to reuse in the battery industry. For this purpose, several critical process parameters such as pressure and temperature are investigated to achieve high recycling efficiencies under feasible conditions.
Electrolyte recovery
The electrolyte in the LiB is a complex system usually composed of a conductive salt dissolved in a matrix of various solvents and additives. The most recent results reported by CHA on sub- and sc-CO2 research show that at low pressure and temperature conditions, the non-polar electrolyte components (almost 66% of the electrolyte) were selectively recovered without the generation of toxic gas emissions, which are typically generated by thermal recovery processes originated by the decomposition of the thermally unstable conductive salt.
In this recycling step, the polar electrolyte components are left in the sample as residues and a subsequent recycling step using suitable cosolvent is required for their selective extraction. During the upcoming phases, researchers will aim to recover the electrolyte completely, including conductive salt and solvents.
In this recycling step, the polar electrolyte components are left in the sample as residues and a subsequent recycling step using suitable cosolvent is required for their selective extraction. During the upcoming phases, researchers will aim to recover the electrolyte completely, including conductive salt and solvents.
The selection of the co-solvent is critically important not only for effective recycling but also for the sustainability and the feasibility of the developed processes. To assess the suitability of the sc-CO2 process, its environmental impact and economic competitiveness, CHA researchers explored also other solvents, which allowed them to select the most promising candidates for future research.
In the upcoming months, CHA will study the effects of co-solvent modified sc-CO2 system parameters on the recycling efficiency of PVDF and the structural properties of the recycled material. Researchers will carry out intensive characterisation studies to clarify the changes in the material structure, to determine the quality, and to optimise the process to reach the reusability goal.
During the first six months, University of Adger [UiA] received three battery packs (out of the five planned) and manually disassembled them, opening for further analysis. In the future, this activity will feed a digital repository as promised in the first delivery of Work package 3.
For each battery pack, the analysis includes:
- a precedence graph informing how components are connected, which, in the upcoming steps, will help determine the best order to dismantle these components automatically.
- an Excel table listing the characteristics of each type of component other than geometrical characteristics: number of items, mass, material, or other specific features.
- 3D scanning in the form of point clouds (pcls) to provide information on the geometry and texture of the components constituting the different battery packs. After testing several hardware and algorithms, two of them have been selected.
In parallel, several of the main important tools have already been identified based on the manual disassembly of these three battery packs, and a tool changer is under development. End effectors (tools) will be able to be changed quickly, including their connection to their power source (electric and/or pneumatic) and their signals.
In addition, the disconnection of power and signal cables using non-destructive methods – operation identified as critical, has been investigated and currently, a concept is prototyped and evaluated. The main challenge is to design a tool that “fits them all”. Additional activities carried out within WP3 have investigated different sorting (characterisation) methods, based on temperature, mass loss, and other flaws, such as deformations, leakage, trace of heat damages.
Safety has also been an important part of the work completed within WP3 during the first six months. A complete monitoring system and a set of safety measures to be followed during the scheduled demanufacturing (discharge, sorting and disassembly) activities have been established.
During February, when the researchers started examining the available methods for automatic task planning using search algorithms and/or reinforcement learning, the robotic system adaptability was discussed. In anticipation of the implementation and testing phases of these adaptive robotic methods, thorough battery knowledge stored within the digital repository must first be developed.