News
Unlocking the Future: 3D Scanning, adaptive planner, and tool design for Automated demanufacturing of LIBs
26/09/2023
Three dimensional (3D) Scanning of Battery Packs
Following the manual dismantling of various battery packs during the first six months of project, researchers at University of Agder (UiA) have developed a semi-automated process to address the diverse nature of battery packs. Their advanced robotic system can estimate the size of individual components of a battery pack. Afterwards, using different angles, it identifies optimal locations to capture precisely 3D images of these components, thus ensuring no detail is missed through this comprehensive scanning.
Using different perspectives, this thorough scanning process is further translated into a list of point clouds. Applying sophisticated algorithms, these point clouds are later combined and merged into a solid mesh component. This process is repeated individually for each new component which needs to be scanned.
Beyond geometric characteristics
While geometric characteristics are important, they provide even greater value when combined with other physical attributes and interconnection data of the components. The researchers have successfully documented these details, resulting in a rich digital repository of the battery pack. With the establishment of this detailed digital repository, the focus is now shifting towards its applications, where the primary goal is to automate the disassembly sequences.
Simultaneously, the team is also focusing on the automatic characterisation of battery packs and modules. Significant efforts are channeled towards creating a robust digital simulator, which will serve as a platform for training and rigorous testing of the disassembly planner – currently under development.
Innovation in disassembly tools
At the same time, the research team involved in work package 3 have been working on improving the disassembly operations tools. The results reported positive feedback, with several tools already successfully tested in lab environment. This is a significant step towards the fully automated disassembly process.
A noteworthy development is the automation of the non-destructive disconnection of cables. This procedure is essential as it stands as the second most frequent operation in battery pack disassembly, just after the unscrewing operation.
You can read more about previous activities developed in work package 3 in the article ‘Manual dismantling of a battery pack‘.
News
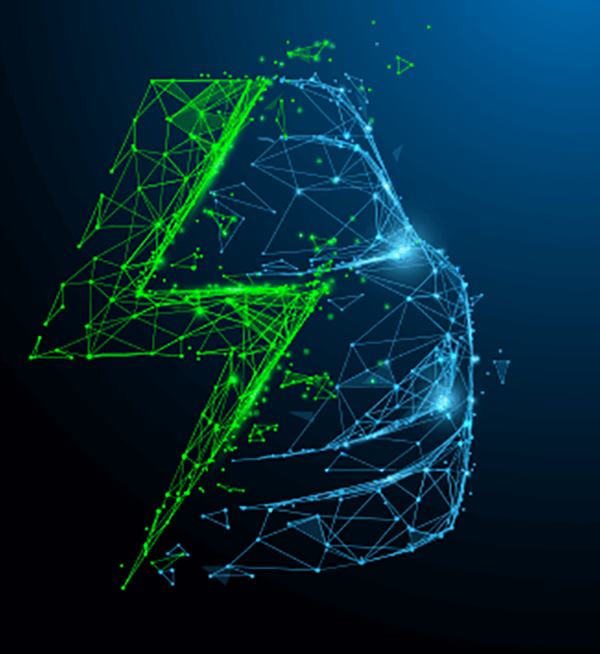
