News
Robotic Demanufacturing of Electric Vehicle Batteries in a Simulation Environment
26/03/2024
Benefits of “offline programming”
Simulation environments have been widely used in robotics for demonstration and planning purposes. This typically takes place within a simulation software or any other platform that can replicate the robot’s dynamics, workspace and surrounding environment, and enable robotic programming. This replication system has proved to be cost- and time-efficient due to a series of advantages: no risk of disrupting the production by removing the robot from the production line, high flexibility allowing infinite number of configurations on a virtual model of the robot, reduced risk of equipment damage due to high predictability of malfunctions. For instance, operational industrial robots can be tested in a simulation environment before deployment. This process is often referred to as “offline programming”.
Researchers at Department of Engineering Sciences, University of Agder have been designing a simulator within a virtual environment to visualise and test various demanufacturing approaches for battery packs, allowing them to collect necessary data such as process duration, disassembly tools – all without the need of physical experiments. This innovative exploration not only streamlines data gathering but can also help identify and remove unforeseen bottlenecks in the disassembly process.
Environment configuration and use case application for battery pack demanufacturing
Using a simulation environment, known for its high-fidelity graphical capabilities, researchers at UiA were able to create a controlled virtual space ideal for visualising complex robotic processes and interactions related to demanufacturing electric vehicle (EV) batteries. The robotic cell design is decomposed across all the subtasks/segments of the disassembly process, with specific consideration to safety aspects and optimised efficiency and accessibility of robotic manipulators.
In order to study in depth and to demonstrate the efficacy of a proposed fully automated demanufacturing line, researchers at UiA meticulously recreated a virtual environment where they simulated the disassembly of a an EV battery pack. This simulation encompasses the entire process from automated discharging to the disassembly of packs into modules, subsequent characterisation, sorting, and finally, the disassembly of modules into individual cells. All elements of the simulation are animated using the simulation platform and a robotic operating system code, providing a holistic view of the potential automation within the demanufacturing process.
For this particular use case, researchers at UiA have calculated the time individually for each disassembly operation, reaching roughly between 12 and 14 minutes for the entire process.
The findings of this research that replicated the complete demanufacturing of EV LiB pack in a virtual, yet realistic industrial setting, illustrate the leverage of automated processes over conventional approaches conventionally relying on manual techniques. The simulation provides estimates for operation time for a given disassembly procedure (disassembly sequence and disassembly process). Upcoming steps will involve AI to generate and optimise the procedures. Additionally, the simulation can identify solutions to minimise human exposure to potential hazards associated with battery disassembly processes. Future in depth and multidisciplinary research is required to optimise the disassembly sequences and process in the simulated environment by training reinforcement learning agents and including a collision avoidance system, to name a few.
Ultimately, the aim of this research is to anticipate the increasing number of EV batteries that will be decommissioned soon, and to ensure a proper management of waste, while recovering all the resources available in clean mobility technologies.
Discover UiA’s previous activities
© Photo: Adobe
News
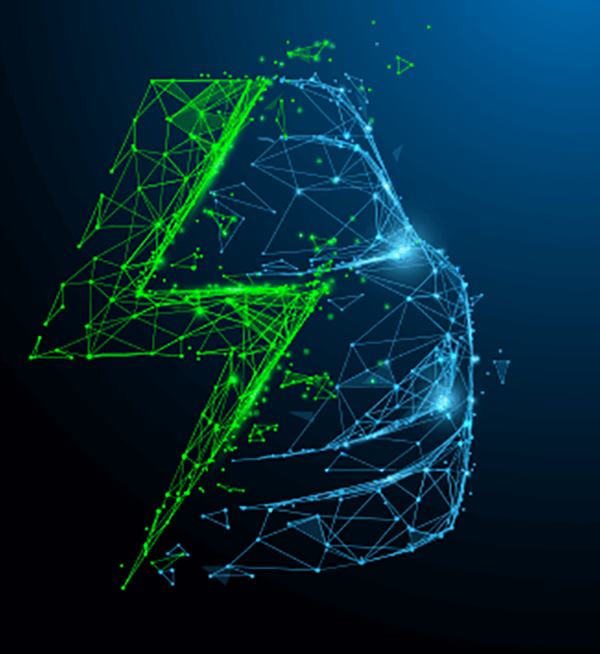
