News
Pre-treatment optimisation
29/04/2025
The challenge of recycling lithium-ion batteries
Current battery recycling is confined to recovering raw materials from the scrap produced by gigafactories. But with the adoption of lithium-ion batteries (LIBs) increasing, a much richer vein will soon emerge, as the first wave of electric vehicles (EVs) reach the end of their lives. And with it, an additional challenge emerges managing the growing waste generated by these energy storage applications. Traditional recycling methods, such as pyrometallurgy and hydrometallurgy, have faced certain hurdles in efficiently recovering valuable materials, mainly due to the presence of the organic components present in the battery binders and separators. Some methods are labour-intensive, whereas others need lots of energy or are environmentally harmful. But each hurdle is another opportunity for innovation.
Optimisation of shredding pre-treatment: TES develops and validates their mechanical process for battery recycling
Leveraging over 20 years’ experience in battery recycling, TES partners oversee the development of a shredding process for batteries using its patented in-house technology. Over the first two years of the RHINOCEROS project, they have been conducting various activities using commercial battery packs, from evaluation and deactivation to pack-to-cell dismantling.
TES have been prioritising safety measures and efficiency, ensuring the system extracts the residual energy stored in batteries, preventing it from going to waste. Following the discharge process, TES applies its proprietary mechano-physical pre-treatment, which involves pre-shredding under an inert atmosphere. This is followed by physical separation techniques to recover polymers, base metals (Al, Cu, Fe), and black mass containing valuable active materials such as Co, Ni, Mn, Li and graphite.
Despite the effectiveness of the current mechano-physical treatment, TES has identified areas for improvement. Moving beyond the state-of-the-art [SoA], TES has optimised its process with a pre-drying step to minimise solvent residues and enhance delamination and separation efficiency. These advancements have led to significant improvements in material recovery and product quality, making the recovered black mass more suitable for downstream hydrometallurgical processing.
- Electrolyte recovery rate: exceeding 95 %
- Polymer recovery rate: exceeding 80 %
- Lithium recovery rate: surpassing 95 %, with the majority retained in the black mass
- Impurity levels of Cu and Al: reduced below 1 %
Optimisation of thermal pre-treatment process
However, reintegration of cathodic and anodic materials into the production chain of new batteries remains a challenge. Thermal pre-treatment of the batteries remains paramount in deactivating, releasing and separating the battery materials. But before reaching the thermal pre-treatment, batteries undergo a sorting process according to the cell type. Discharging is not mandatory prior to the pre-treatment.
ACCUREC [ACC] partners have been modifying their thermal pre-treatment process, including a preceding stage for cell solvent recovery, which places their process beyond the SoA. To explore this technological path, they experimented various parameters altering the working temperature and the pressure of solvent distillation, to address safety concerns and stabilise the background electrolyte. A selective recovery of solvent was possible under specific temperature and pressure conditions achieving high purities >99.6 %. However, additional refining steps are necessary prior to further use in battery manufacturing. ACC partners managed to deactivate batteries completely and produce high-purity black mass [BM] with recovery yields of >95 %, using high temperature pyrolysis and a two-stages screening process.
Their process demonstrates that the distillation process prior to the thermal treatment allows the extraction of solvents used in the cell and streamlines high recovery rates of active material. However, their research concludes that the processing of end-of-life [EoL] batteries remains a trade-off between recycling efficiency and purity of the obtained fractions due to the large number of compounds and lack of control over the starting material.
Electrolyte recycling
The safe and environmentally responsible recovery of electrolytes is crucial in the LIBs recycling process. The SoA non-aqueous liquid electrolytes consist of a conductive salt (lithium hexafluorophosphate, LiPF6) dissolved in a mixture of organic solvents and additives. Many of these components are highly volatile, flammable, and classified as toxic. The current state-of-the-art LiB recycling process begins with the production of black mass, obtained through a series of pre-treatment steps. But uncontrolled evaporation of volatile electrolyte solvents during these stages presents major safety hazards. The research group at Technical University of Chalmers [CHA] have been exploring various processing pressure and temperature parameter settings for their supercritical carbon dioxide [scCO2], with a particular focus on the extraction of ethylene carbonate [EC].
CHA researchers successfully developed and validated the scCO2 process for electrolyte recycling from LIB black mass. The results demonstrated a >95 % overall recovery, with individual yields of >99 % for DMC, EMC, and DEC and 95 % for EC, using specific process conditions. The recovered EC retains its original structural integrity, confirming its chemical stability and purity.
But beyond the high purity and selectivity of carbonates, the developed scCO2 does not require any chemical reagents. Moreover, the used CO2 can be indefinitely recycled within the system, turning it into a clean separation process that eliminates toxic gas during processing.
Reactive milling for black mass production
The research group at KIT received black mass samples from partners ACC and TES. Only the samples from TES were fit to study the mechanochemical transformation of BM, as the ACC supply was already in a reduced state. The BM supplied by TES consists mostly of NMC (lithium nickel manganese cobalt oxides) cathode material and graphite, which was found to slow down the reaction kinetics.
KIT researchers applied their reactive milling on the BM provided by TES to reduce the cathode material to its metallic form and produce water-soluble lithium salts. They optimised the process using three types of mills [two planetary mills of different sizes and a SPEX shaker mill], engaging three types of reagents: Al, Mg and Ca. They also investigated the influence of milling parameters on the process duration and identified the most optimal parameters for faster kinetics. The planetary mill showed better results than the shaker mill for Mg and Al, while Ca performed well in the SPEX mill.
In depth studies performed by KIT concluded that the process is a mechanically induced self-propagating reaction, which is initiated by mechanical energy, such as the impact energy from the milling balls. Once started, it propagates through the material on its own, similar to a chain reaction. This type of reaction is highly exothermic, releasing a significant amount of heat, which further drives the reaction forward. Small amounts of volatile compounds, such as residual solvents or moisture, were found to have a significant effect on the reaction time. The basis of the volatiles interference is not clear yet, but it seems to be important to remove these compounds before the milling process to ensure a more efficient and faster reaction.
Further experiments are needed to scale up the process and ensure that it can be applied to larger batches.
Vacuum pyrolysis and Supercritical CO2 [scCO2] processing for binders recovery
Binders such as polyvinylidene fluoride [PVDF] and polytetrafluoroethylene [PTFE] for cathodes, and carboxymethyl cellulose [CMC] and styrene-butadiene rubber [SBR] for anodes, are particularly difficult to separate during mechanical processing. This reduces the efficiency of metal recovery and can lead to the formation of environmentally harmful substances, such as per- and polyfluoroalkyl substances [PFAS].
Thermal treatment methods, while effective in removing these organics, generate hazardous emissions like hydrogen fluoride [HF] and phosphoryl fluoride [POF3], necessitating stringent gas treatment measures. Additionally, battery separators, often composed of complex polymers like polyethylene [PE] and polypropylene (PP), pose further challenges due to their low economic value and the presence of residual hazardous materials.
ACC has optimised vacuum pyrolysis at 550°C, which enabled the complete decomposition of PVDF, and thus, the effective removal of binders and separators from LIB waste, while recovering fluorinated compounds from decomposition products. Generated HF was captured using two different methods: through potassium hydroxide [KOH] washing (producing potassium fluoride [KF]) or a calcite filter (producing fluorite).
Supercritical carbon dioxide [scCO₂] process technology has emerged as a promising alternative for LIB recycling, offering properties that are adjustable to organic compounds. However, PVDF dissolution in scCO₂ alone requires extreme conditions, making industrial implementation challenging. Chalmers researchers have explored possible co-solvent scCO₂ systems to enable the recycling of binder directly from mechanically treated BM. They developed a specialised extraction process using scCO₂ with a co-solvent (dimethyl sulfoxide, DMSO) to recover the PVDF binder from industrial battery waste. The process achieved a 55.6 % recovery rate of PVDF under mild conditions.
The scCO₂ technology was also applied to electrolyte and separator recycling, achieving over 90 % separator recovery with high purity.
© visual: ImageFlow via Adobe Stock
News
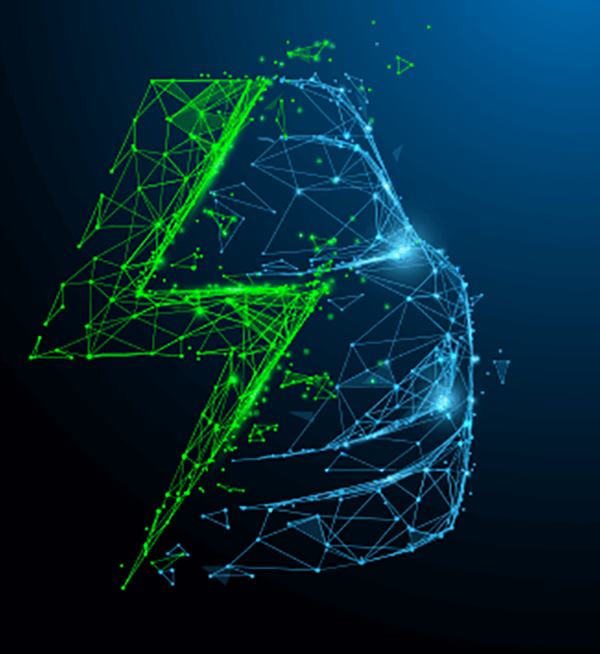
