News
On Monday, 10 July 2023, the Council of the European Union adopted a new regulation that strengthens sustainability rules for batteries and waste batteries. This regulation covers the entire life cycle of batteries, ensuring their safety, sustainability and competitiveness from production to reuse and recycling.
Read the official press release
Recognising the vital role batteries play in the decarbonisation process and the transition towards zero-emission mobility, Teresa Ribera, Spanish Minister for the Ecological Transition reinforced the Presidency’s commitment to supporting comprehensive regulation encompassing all types of batteries. This includes waste portable batteries, electric vehicle batteries, industrial batteries, starting, lightning and ignition (SLI) batteries primarily used in vehicles and machinery, as well as batteries for light means of transport like electric bikes, e-mopeds, and e-scooters.
“At the same time end-of-life batteries contain many valuable resources and we must be able to reuse those critical raw materials instead of relying on third countries for supplies. The new rules will promote the competitiveness of European industry and ensure new batteries are sustainable and contribute to the green transition.”
| Teresa Ribera, Spanish Minister for the Ecological Transition
To foster a circular economy, the regulation establishes requirements for the end-of-life phase, including collection targets and obligations, material recovery targets, and extended producer responsibility. Dedicated collection objectives for waste batteries used in light means of transport will be implemented, aiming at 51% by the end of 2028, respectively 61% by the end of 2031. Furthermore, the regulation sets mandatory minimum levels of recycled content for industrial batteries, SLI batteries and electric vehicle batteries. The following initial values have been established:
- 16% for cobalt
- 85% for lead
- 6% for lithium
- 6% for nickel
Additionally, batteries will also be required to hold documentation proving their recycled content.
To improve the functioning of the internal market for batteries and ensure fair competition, the regulation introduces safety, sustainability, and labelling requirements. It includes provisions for battery labelling and information disclosure, including details on battery components and recycled content. Additionally, an electronic “battery passport” and a QR code will be implemented to enhance traceability and transparency. These labelling requirements will take effect by 2026, while the QR code implementation is expected by 2027, providing member states and manufacturers with ample time to prepare.
This new regulation aims to mitigate environmental and social impacts throughout the battery’s life cycle. By establishing strict due diligence rules for operators, the EU is ensuring operators are bound to verify the source of raw materials used for batteries placed on the market. However, the regulation provides for an exemption for SMEs from the due diligence rules.
After its signature by the Council and the European parliament, the new regulation will be published in the EU’s Official Journal, expecting to enter into force 20 days after.
RHINOCEROS project in the current legislative framework
Launched in 2022, the RHINOCEROS project fits within the current framework recently adopted by the Council of Europe under the Spanish Presidency. Designed to support the raw materials supply, the RHINOCEROS project will demonstrate a smart sorting and dismantling robot at TRL6, enabling the automation of a battery repurposing production line. When direct reuse and repurposing of batteries is not possible, RHINOCEROS will investigate several ground-breaking circular recycling routes aiming at the recovery of all materials present in LIBs (e.g., metals, graphite, fluorinated compounds, electrolytes, polymers, and active materials).
A first set of conclusions stemming from the research of our partners generated a database and the parameters for module selection, which will further facilitate the development of electric vehicles 2nd life batteries.
Read more in the article “Acceptance criteria and guidelines for 2nd life prone LIBs”
The infographic can be accessed on the Council of the European Union’s website using this link.
Aiming towards a zero-waste strategy for the recovery of metals from battery refining waste waters, LEITAT is working on the development and evaluation of novel polymer inclusion membranes (PIM). PIMs are a type of liquid membrane in which the liquid phase, the extractant, is held within a polymeric network. The interest in these membranes has been growing exponentially over the past few years as an alternative separation technique to conventional solvent extraction.
Work during the first six months has focused on the evaluation of different extractants for the target metals: lithium, manganese, cobalt and nickel. Researchers established a liquid-liquid extraction protocol based on two different processes in which the target metal is extracted and recovered separately. During the extraction step, a specific carrier compound selective towards the target metal separates an amount of it from a feed metal solution. The recovery of the metal takes place in the second process, where a stripping solution is employed to recover the metal previously extracted through the carrier. Initial PIMs containing the most efficient extractants have been prepared, characterised and are currently evaluated. The featured image depicts the continuous procedure used to test the synthesised PIMs.
The current industrial pre-treatment and downstream processes (e.g., pyrolysis, calcination, etc.) are still inefficient and have significant limitations. Plastics and electrolytes sacrificed in the initial stages of the recycling process are overlooked when it comes to their recovery. Within the RHINOCEROS project, Chalmers University [CHA] is working on recycling of ignored content of the LIBs waste, electrolyte and polymeric materials by developing an innovative process based on Supercritical Carbon Dioxide (sc-CO2) technology.
Due to its environmental friendliness, non-toxic, low cost and straightforward processing features, the sc-CO2 technology has been attracting both scientific and industrial interest. With consistent leverage over other processes, sc-CO2 technology is already widely used in various industries including food, cosmetic and pharmaceutical industries [i.e., to decaffeinate coffee or tea, extract vegetable oils etc.] Although it has many applications, its use in battery recycling was recently discovered and the Chalmers research group is one of the pioneers in this field.
Within the project’s framework, CHA researchers are targeting the development of the sc-CO2 extraction process which will selectively recycle the electrolyte and the polymeric material from the LiB waste. The electrolyte, binder, and separator will be recycled in subsequent steps and purified to reuse in the battery industry. For this purpose, several critical process parameters such as pressure and temperature are investigated to achieve high recycling efficiencies under feasible conditions.
Electrolyte recovery
The electrolyte in the LiB is a complex system usually composed of a conductive salt dissolved in a matrix of various solvents and additives. The most recent results reported by CHA on sub- and sc-CO2 research show that at low pressure and temperature conditions, the non-polar electrolyte components (almost 66% of the electrolyte) were selectively recovered without the generation of toxic gas emissions, which are typically generated by thermal recovery processes originated by the decomposition of the thermally unstable conductive salt.
In this recycling step, the polar electrolyte components are left in the sample as residues and a subsequent recycling step using suitable cosolvent is required for their selective extraction. During the upcoming phases, researchers will aim to recover the electrolyte completely, including conductive salt and solvents.
In this recycling step, the polar electrolyte components are left in the sample as residues and a subsequent recycling step using suitable cosolvent is required for their selective extraction. During the upcoming phases, researchers will aim to recover the electrolyte completely, including conductive salt and solvents.
The selection of the co-solvent is critically important not only for effective recycling but also for the sustainability and the feasibility of the developed processes. To assess the suitability of the sc-CO2 process, its environmental impact and economic competitiveness, CHA researchers explored also other solvents, which allowed them to select the most promising candidates for future research.
In the upcoming months, CHA will study the effects of co-solvent modified sc-CO2 system parameters on the recycling efficiency of PVDF and the structural properties of the recycled material. Researchers will carry out intensive characterisation studies to clarify the changes in the material structure, to determine the quality, and to optimise the process to reach the reusability goal.
During the first six months, University of Adger [UiA] received three battery packs (out of the five planned) and manually disassembled them, opening for further analysis. In the future, this activity will feed a digital repository as promised in the first delivery of Work package 3.
For each battery pack, the analysis includes:
- a precedence graph informing how components are connected, which, in the upcoming steps, will help determine the best order to dismantle these components automatically.
- an Excel table listing the characteristics of each type of component other than geometrical characteristics: number of items, mass, material, or other specific features.
- 3D scanning in the form of point clouds (pcls) to provide information on the geometry and texture of the components constituting the different battery packs. After testing several hardware and algorithms, two of them have been selected.
In parallel, several of the main important tools have already been identified based on the manual disassembly of these three battery packs, and a tool changer is under development. End effectors (tools) will be able to be changed quickly, including their connection to their power source (electric and/or pneumatic) and their signals.
In addition, the disconnection of power and signal cables using non-destructive methods – operation identified as critical, has been investigated and currently, a concept is prototyped and evaluated. The main challenge is to design a tool that “fits them all”. Additional activities carried out within WP3 have investigated different sorting (characterisation) methods, based on temperature, mass loss, and other flaws, such as deformations, leakage, trace of heat damages.
Safety has also been an important part of the work completed within WP3 during the first six months. A complete monitoring system and a set of safety measures to be followed during the scheduled demanufacturing (discharge, sorting and disassembly) activities have been established.
During February, when the researchers started examining the available methods for automatic task planning using search algorithms and/or reinforcement learning, the robotic system adaptability was discussed. In anticipation of the implementation and testing phases of these adaptive robotic methods, thorough battery knowledge stored within the digital repository must first be developed.
Focusing on mechanochemical (MC) processing, the chemical transformation of the black masses (BMs) supplied by partners ACCUREC and TES, is planned to be carried out within Work package 4.
Before MC processing, the black masses were analysed using a combination of different analytical techniques. Both quantitative and qualitative analysis were undertaken to determine the Lithium and transition metals yield of the developing recycling process.
Using different reducing agents such as Al, Ca, and their mixtures, researchers carried out preliminary investigations of the MC processing of BMs. Within this task, different aspects, such as the role of the ball milling conditions, the ball milling time, presence of other nonreactive components, and nature of the reducing material were investigated. The analysis led to the conclusion that the kinetics of the MC-induced reduction reaction is sensitive to multiple processing parameters, as shown in the featured image:
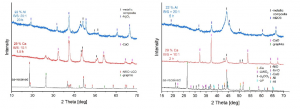
XRD patterns of the as-received BMs and products of their reduction after MC processing with Al and Ca as reducing agents: left-TES material; right-ACC material
The upcoming research will focus on improving the reduction reaction kinetics and eliminating the possible safety hazards of fine powder materials. Once finalised, this work will determine the optimal ball milling conditions to be scaled up.
Recovery of Lithium as battery grade materials
The process described in Task 4.4 leads to the chemical transformation of the black masses (BMs) into ferromagnetic Co-, Ni- and Mn-containing products, which will be separated from other by-products. Lithium will be extracted from the rest of the solid products in the subsequent aqueous leaching process to be further transformed into battery-grade lithium carbonate (Li2CO3) salt.
Within the M1-M6 period, aqueous leaching of the ball-milled samples using Al and Ca as reducing agents (RA) was carried out. At a preliminary stage of investigations, researchers noticed the resulted Li2CO3 materials presented small amount of impurities.
To increase the yield of lithium recycling, in the upcoming period, the research work will target the improvement of the leaching conditions and the purification process.
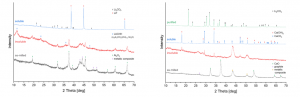
X-ray diffraction patterns of the as-milled BM obtained from TES, products of their reduction reactions after MC processing with Al (left) and Ca (right) as RA, and obtained Li salts after aqueous leaching
Within Work package 2 – Selection, characterisation and supply, partners Watt4Ever [W4E] and Accurec [ACC] assembled the database and the parameters for module selection, which will further facilitate streamline the development of electric vehicles (EV) 2nd life batteries.
The criteria were selected based on the 2nd life partner input and were adapted at module level. Partners generated a database using a sample of 200 commercial and passenger vehicles grouped in the following categories: Battery Hybrid Electric Vehicle (BEV), Mild Hybrid Electric Vehicle (MHEV) and Plug in Hybrid Vehicle (PHEV). The input received contributed to the identification of the required acceptance criteria that will help select the best modules for 2nd life Battery Energy Storage System (BESS).
Selection criteria
The database of 200 BEV/PHEV/MHEV batteries and their characteristics, including a summary of technical information for each model, has been generated. Due to the mechanical, technical and software challenges that need to be overcome for efficient module integration in deployable LV and HV BESS, the database includes the following parameters as criteria for 2nd life applications: size, capacity, Cell Management Unit (CMU), casing and cell configuration. The chosen criteria should improve the security of the dismantling process and facilitate access to the module level for each battery pack. Simultaneously, these parameters will simplify the integration of 2nd life modules in battery energy storage or other systems.
Mechanical design criteria | Electrical design criteria |
Physical Properties | Cell configuration |
Capacity | Casing |
BMS/CMU |
Mechanical design criteria
For 2nd life applications, module level parameters are the ones that give insight on the desirability. First set of parameters are the Physical Properties. Second life integrators already have knowledge of module integration and have specific designs to accommodate the battery modules, if the module sizing is the commonly used roughly the size of a shoe box 350*150*120 mm, it already makes the integration a lot easier, faster and cheaper. By adding Capacity, power density can be calculated, and thus the technical design can be improved to maximise the capacity of the system.
Electrical design criteria
Cell configuration give an insight in to the voltage of the module, but also allows to wonder about the possible Battery Management System (BMS) use in the battery. Casing protects the cells from puncture, grinding, shorting out, but most importantly, expansion. With regards to BMS,/CMU, on various cases, partners noticed that OEMs integrate internal CMU on the module level, which can facilitate their use for second life applications. On the contrary, in cases where no CMU is available, one needs to be provided by the OEM or 3rd party.
Module acceptance criteria for low voltage (LV) 48V systems
This design would allow to accommodate shoebox size modules from different OEM, while also keeping the same design of the box with small adjustments.
Mechanical design criteria
- Casing– Open top or Alu Jacket
- Size: 350*150*120 mm ± 100 mm on all axis
- CMU: External multimodule, external single module or internal and all can be reused if OEM CMU unit communications gateway is possible.
- Cell amount: 3s-12s
- Voltage: 10V-30V
- Chemistry: NMC with risk mitigation or LFP
Module acceptance criteria for high voltage (HV) system
For HV battery energy storage system, modules with higher voltage are prioritised, due to their capacity to save time and budget otherwise spent on wiring and building expenses. External CMU from 3rd party is the preferred solution to internal CMU, as it minimises any interference and bug risks with the Energy Management System. to be used to minimize any interference and bug risks with the Energy Management System.
- Size: >350*150*120 mm ± 100 mm on all axis
- Cell amount: 12s-30s
- Voltage: 40V-100V
TECNALIA [TEC] has actively undertaken both the coordination tasks and the experimental activities that correspond to the solvometallurgical treatment of the received black masses. Firstly, the coordination of the project started with the preparation of the kick-off meeting, in which the entire Consortium assembled in San Sebastián (Basque Country – Spain) and comprises administration and management to ensure an efficient development of RHINOCEROS project.
Also, the experimental section concerning the critical materials extraction from the received black masses from spent batteries started out after receiving the samples from partners ACCUREC [ACC] and KIT.
After characterisation, TEC performed a first round of tests to these samples using a solvometallurgical route and assessing pre-treatment effect on the process. In parallel, State of Art is analysed for different relevant solvometallurgical systems aiming lithium recovery. New batches of experiments will be performed for process optimisation and new tests will also be performed when further black mass samples are received.
VITO has developed the Gas-Diffusion Electrocrystallisation (GDEx) technology for various metal extraction processes. The GDEx technology utilises gas-diffusion electrodes to recover and synthesise different electrodic materials in the form of precipitates containing the desired metals. This process has shown promising results in metal recovery and selectivity, particularly for different metal extraction process.
The GDEx team has conducted experiments with synthetic solutions to optimise the metal recovery yield and selectivity by investigating the effect of different metal precursor solution to the process. Once the GDEx process is optimised with synthetic streams and the precipitating mechanisms are better understood, the team plans to extend the process to various spent battery waste products obtained from consortium partners. The process will involve precipitation in the form of layered-double hydroxides, and the team will investigate the downstream steps required to obtain recycled battery-cathode material. This is an important step towards sustainable and environmentally friendly practices in the battery industry.
Find out more information about the GDEx process at http://gdex.vito.be
Publication: Synthesis of material libraries using gas diffusion electrodes. Mater. Chem. A, 2020,8, 11674-11686
Between 14 and 18 November 2022, the European Commission organised the 7th edition of the Raw Materials Week, gathering a wide range of stakeholders discussing policies but also relevant alternatives in the field of raw materials. This was an opportune occasion for the RHINOCEROS project to cluster with seven other EU-funded projects at the event “Production of raw materials for batteries from European sources”. The objective of the workshop was to create an environment that could foster knowledge exchange on different approaches for the recycling and recovery for battery applications. Co-organised by CROCODILE, RHINOCEROS and LICORNE, with the participation of the EU funded projects BATRAW, RESPECT, RELiEF, FREE4LIB and ENICON, the workshop gathered nearly 100 organisations driving the production and the recycling of raw materials for battery applications from primary and secondary resources.
Due to the increasing usage of batteries for electric vehicles (EVs) and energy storage systems generated by the EU’s mission to limit climate change, the demand for many metals relevant for batteries is expected to grow by more than 1000% by 2050. Held in a hybrid format, the workshop provided participants with the opportunity to discover innovation routes followed by the clustering projects on their pathway to secure sustainable and responsible sourcing of raw materials for battery production.
Nearly three hours packed with presentations provided stakeholders with essential information about each project, from the main objectives and expected outcomes, to the lessons drawn from the activities carried out.
The CROCODILE project – First of a kind commercial Compact system for the efficient Recovery of Cobalt Designed with novel Integrated Leading technologies– was presented by Dr. Lourdes Yurramendi (TECNALIA). As the most mature project, CROCODILE’s keynote focused on valuable findings and learnings regarding different aspects of the project: the samples treatment, the selection of flowsheets, the life cycle analysis (LCA) and cost (LCC) of the pilot unit, to name only a few. Later on Monday, the project was also featured as a Success Story in the Raw Materials Week, where the presentation video was played for the first time.
Download the CROCODILE presentation
Sonia Matencio Lloberas (LEITAT) presented the BATRAW project – Recycling of end-of-life battery packs for domestic raw material supply chains and enhanced circular economy. This project will develop and demonstrate two innovative pilot systems for sustainable recycling and end-of-life (EoL) management of EV batteries. Depending on the results obtained, these technologies could be extended to other types of batteries to recover all the metals and materials contained: i.e., cobalt, nickel, manganese, lithium, graphite, aluminium, and copper.
Download the BATRAW presentation
Nader Akil (PNO Innovation Belgium) explained the mission and the motivation behind the RHINOCEROS project – Batteries reuse and direct production of high performances cathodic and anodic materials and other raw materials from batteries recycling using low cost and environmentally friendly technologies. As attractive energy storage technologies, Lithium-ion batteries (LIBs) have proven to be a reliable solution, especially when it comes to the production of low-emission fleets (EVs), followed by stationary storage market and consumer electronics. According to the Strategic research Agenda for Batteries, by 2030, the global demand for LIBs is estimated to increase 14 times and the EU could account for 17%. The battery market is expected to reach 250 billion EUR/year by 2025, while the production in Europe is foreseen to rise to 300 GWh/year as of 2030. This generates opportunities for projects like RHINOCEROS to develop economically and environmentally viable routes for re-using and recycling EoL EVs and stationary energy storage Lithium-ion batteries (LIBs).
Download the RHINOCEROS presentation
Similar to the RHINOCEROS project, FREE4LIB [Feasible recovery of critical raw materials through a new circular ecosystem for a Li-ion battery cross-value chain in Europe] aims to simplify the recycling process of LIBs, as a more resilient and environmentally friendly alternative to the current linear economic model – take, make, dispose. The project, presented by Juan Castro (CARTIF), will develop six technologies at TRL5 to achieve new sustainable and efficient processes to recycle EoL LIBs: dismantling, pre-treatment and four materials recovery processes aiming to reach highly efficient materials recovery (metal oxides, metals and polymers). Additional to the recycling solutions, FREE4LIB will also target three processes dealing with metals and polymers re-using and electrode synthesis to re-manufacture new LIBs.
Download the FREE4LIB presentation
Justo Garcia (Orano Mining) presented the RESPECT project. Funded by the Horizon Europe research and innovation programme, the project aims to strengthen expertise in techniques and the value chain for the recycling of electric vehicle batteries at European level. The RESPECT project will develop a global process encompassing a process-chain flexible enough to treat all kinds of batteries in closed loop. Precisely, researchers will explore two recycling routes: full hydrometallurgy and direct recycling, and an improved Life Cycle Assessment of each recycling segment to reduce emissions, health risks and safety issues.
Download the RESPECT presentation
Recently launched, the LiCORNE project – Lithium recovery and battery-grade materials production from European resources, was introduced by Alan González Morales (PNO Innovation Belgium), who explained briefly the project’s ambitious objectives to establish the first-ever Li supply chain in Europe. With five large primary resource owners (including one of the world leaders in Li production) involved in the consortium, the project aims to increase European Li processing and refining capacity for producing battery-grade chemicals from ores, geothermal and continental brines, tailings and off specification battery cathode materials (waste).
Download the LiCORNE presentation
Gabriel Hidalgo, from the Recycling Unit of Avesta Battery & Energy Engineering (ABEE), outlined the objectives and the impact expected from the RELiEF project – Recycling of Lithium from Secondary Raw Materials and Further. Expected to boost the recycling industry, this project aims to reduce Li waste by more than 70%, and to transform recycled resources into high value battery-grade material. Relying on a very diversified consortium, RELiEF will additionally propose a new business model for materials acquisition and processing, taking into consideration environmental and social sustainability.
Download the RELiEF presentation
Sofía Riaño Torres (KU LEUVEN) presented the last EU project, ENICON– Sustainable processing of Europe’s low-grade sulphidic and lateritic nickel/cobalt ores and tailings into battery-grade metals -Launched in June 2022, the project aims to improve the refining capacity of domestic and imported low-grade Ni/Co. ENICON’s metal recovery route using hydrochloric acid dispenses with the old-school hydro-based approach that involves continuously precipitating and redissolving metals. Thus, it reduces the amount of chemicals needed for metal dissolution, which results in the production of potentially harmful waste streams. More information about the project in the joint documentary commissioned together with EU funded project NEMO: Responsible Mining in Europe.
Download the ENICON presentation
The workshop in figures
Although only in its first edition, the clustering workshop Production of raw materials for batteries from European resources attracted a diversified range of stakeholders. Counting more than 150 people registered, the audience was dominated by research organisations (26,97%), the rest of the audience being equally distributed between academia (17,76%), large companies (17,11%), SMEs (16,45%), EU institutions (4,61%) and other stakeholders addressing raw materials – national and regional administrative authorities, logistics service provides, investing companies, trade associations, NGOs, consulting companies (17,76%). Participants are located mainly in Europe but a percentage of nearly 20% shows growing enthusiasm from third countries, such as Turkey, Canada, South Korea, Chile, etc.
Exploring future clustering ideas
With the real peak of valuable outcomes from H2020 projects coming now, the aim goes beyond informing about the progress achieved to date. Building on the knowledge generated so far, new projects need to address different challenges, such as the high cost of exploration activities, the geological uncertainty, and the necessity to develop improved processing and refining technologies for better recovery of minerals and metals from side streams and industrial waste. Such challenges require close collaboration on all levels and across the entire battery value chain.
The last part of the event featured an interactive session, which included seven questions scrutinising stakeholders’ interest for similar clustering initiatives. With favourable answers and reviews, the Production of raw materials for batteries from European resources could turn into a permanent clustering hub fostering knowledge exchange and stimulating synergies between projects. More information will follow soon.
The Cluster Hub “Production of raw materials for batteries from European resources”
After the successful workshop held in November 2022, the participating projects launched in January the cluster hub carrying the same title – “Production of raw materials for batteries from European resources”. The platform is a collaboration-driven community sharing the same mission – to foster the knowledge necessary to drive a more sustainable and circular production of raw materials for the European battery industry.
Photo gallery